Exploring Pressure Die Casting Components: Benefits, Applications, and More
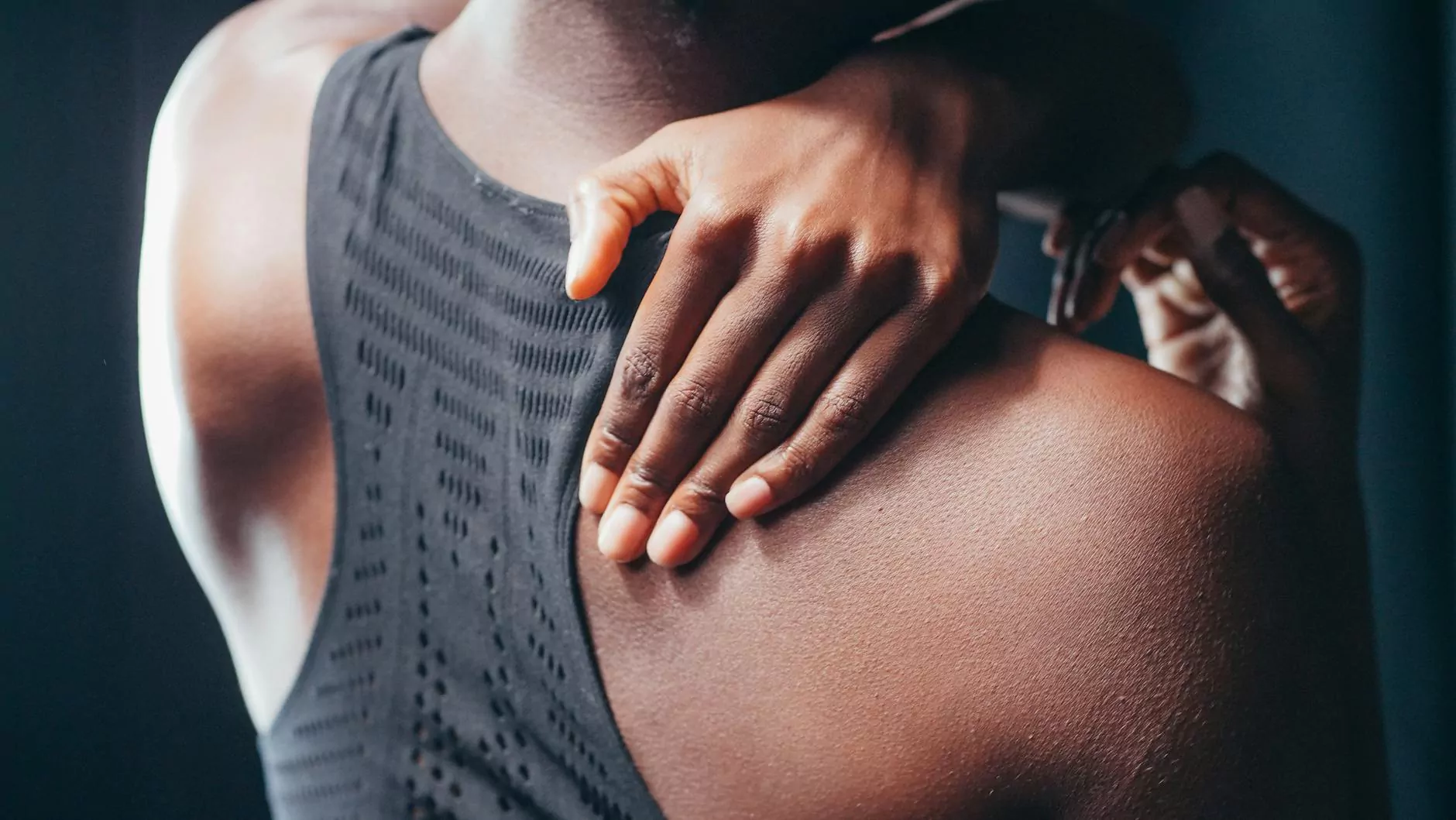
The manufacturing industry has always relied on innovative techniques to enhance efficiency and product quality. One such remarkable process is pressure die casting, particularly known for producing high-quality metal components. This article dives deep into the realm of pressure die casting components, highlighting their significance, applications, and the various benefits they bring to the table.
What is Pressure Die Casting?
Pressure die casting is a metal casting process that forces molten metal under high pressure into a mold cavity. This method is highly regarded for its ability to produce intricate components with excellent surface finish and dimensional accuracy. The process is typically utilized with non-ferrous metals such as aluminum, zinc, and magnesium.
The Pressure Die Casting Process
The pressure die casting process involves several critical stages:
- Preparation of Mold: The mold is prepared, often made of high-strength steel to withstand the molten metal's temperature and pressure.
- Heating the Metal: The chosen metal is melted in a furnace.
- Injection of Molten Metal: Using a hydraulic or mechanical piston, molten metal is injected into the mold under high pressure.
- Cooling and Solidification: The metal remains in the mold to cool and solidify, forming the desired component.
- Mold Opening and Component Extraction: Once solidified, the mold is opened, and the component is ejected.
Benefits of Pressure Die Casting Components
Utilizing pressure die casting components offers numerous advantages:
- High Precision and Accuracy: The high pressure involved ensures that the molten metal fills all crevices of the mold, resulting in meticulously detailed components.
- Superior Surface Finish: Components produced through this method often require little to no finishing work, reducing the overall production cost.
- Mass Production Capabilities: Once the mold is created, producing large quantities of products becomes efficient and cost-effective.
- Diverse Material Options: A wide range of non-ferrous alloys can be utilized, providing designers with great flexibility.
- Waste Reduction: The process minimizes waste when compared to traditional machining methods, leading to a more sustainable production cycle.
Applications of Pressure Die Casting Components
The applications of pressure die casting components are vast and diverse, permeating various industries:
1. Automotive Industry
The automotive sector relies heavily on pressure die casting for producing lightweight components such as:
- Engine blocks
- Transmission housings
- Brackets and support structures
2. Aerospace Industry
In aerospace, the principle of weight reduction serves as a critical factor. Pressure die casting components are sought after for:
- Aircraft structural parts
- Engine components
- Mounting brackets
3. Consumer Electronics
The consumer electronics industry requires precision and durability, making pressure die casting an ideal choice for:
- Housings for devices like laptops and smartphones
- Heat sinks for thermal management
- Connectors and switches
4. Medical Devices
The demand for high precision in the medical field has led to the adoption of pressure die casting components in:
- Equipment housings
- Functional parts for surgical instruments
- Implants and prosthetics
Choosing the Right Metal Fabricator for Pressure Die Casting Components
Selecting the right metal fabricator is crucial to ensure the quality and precision of pressure die casting components. Here are factors to consider:
- Experience and Expertise: Look for fabricators with extensive experience in pressure die casting.
- Quality Assurance Processes: Ensure they have stringent quality control measures in place.
- Technological Capabilities: Advanced machinery and technology can significantly impact the outcome.
- Material Knowledge: Understanding the properties of various metals is essential for selecting the right alloy for your project.
Future Trends in Pressure Die Casting
The landscape of pressure die casting is continuously evolving with technological advancements and innovations. Some future trends include:
- Automation and Robotics: Increased automation will streamline the production process and enhance precision.
- 3D Printing for Molds: The ability to create molds using 3D printing could significantly reduce lead times and costs.
- Sustainability Practices: An increased focus on eco-friendly practices and reduced waste will shape the future of die casting.
Conclusion
In conclusion, pressure die casting components play a vital role in modern manufacturing across various sectors. Their advantages in precision, surface finish, and material versatility ensure that they remain a preferred choice for engineers and manufacturers alike. As technology evolves, the future of pressure die casting looks promising, with innovations paving the way for even more efficient and sustainable practices. If you're looking for a reliable partner in metal fabrication, consider exploring the offerings at deepmould.net for expertly crafted pressure die casting components that meet your specific needs.