Revolutionizing Water Filtration with 3D Printing Technology
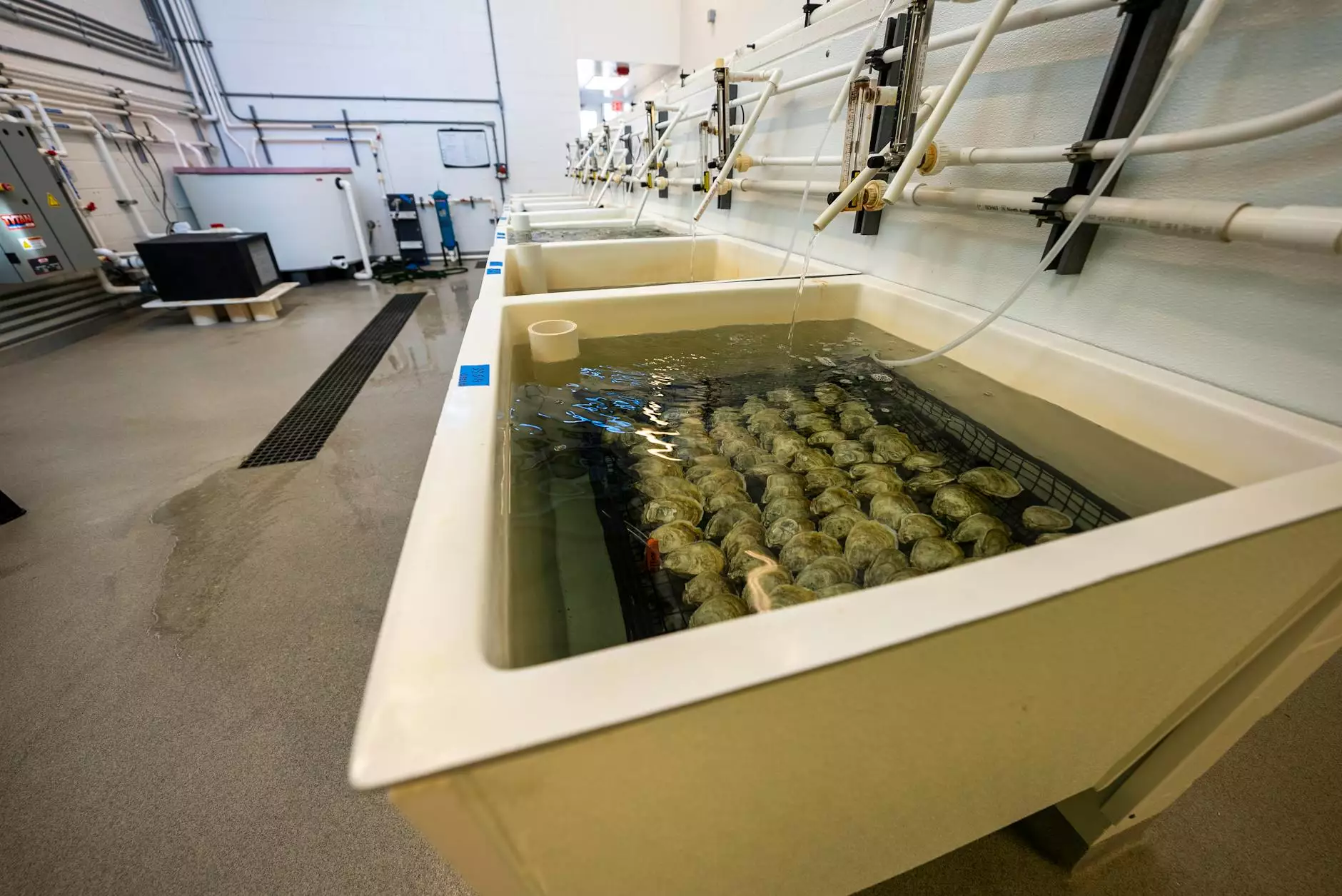
In the rapidly advancing landscape of modern manufacturing, 3D printing has emerged as a game-changer, especially within the realm of environmental sustainability and innovative product development. One of the most promising applications of this cutting-edge technology is the creation of 3d printed water filter systems. These systems are redefining the paradigms of water purification—making them more accessible, customizable, and environmentally friendly than ever before.
Understanding the Potential of 3D Printing in Water Filtration
3D printing, also known as additive manufacturing, involves creating objects layer-by-layer based on digital models. This process opens a plethora of possibilities for producing complex geometries and integrating multiple functions into a single, seamless piece. When applied to water filtration, this means the ability to craft intricate filter components, tailored structures, and innovative materials that optimize filtration performance.
The Advantages of 3D Printed Water Filters
- Customizability: Designs can be easily modified to suit specific water quality issues or local conditions, enabling personalized solutions.
- Cost-Efficiency: Mass production and rapid prototyping reduce manufacturing costs, making clean water more affordable.
- Rapid Innovation: Fast turnaround times mean new filter designs can be tested and improved swiftly.
- Complex Geometries: Create filtration structures impossible with traditional manufacturing techniques—like intricate pore networks or bio-inspired surfaces.
- Sustainable Materials: The ability to use eco-friendly, biodegradable, or recycled materials enhances the environmental sustainability of water filters.
How 3D Printing Enhances the Design of Water Filtration Systems
Designing effective water filters requires meticulous attention to pore size, flow dynamics, and material properties. 3D printing enables engineers and designers to experiment with complex internal structures that optimize these factors:
Optimized Flow Channels
Through advanced CAD modeling, creators can develop channels that direct water efficiently through the filter medium, minimizing pressure drops and maximizing filtration rates.
Innovative Material Use
Exploring materials like porous ceramics, specialized polymers, or composites tailored for filtration enhances durability and contaminant removal capabilities.
Bio-Inspired Structures
Nature offers remarkable models for filtration—like sponges and coral formations. 3D printing facilitates the replication of these intricate patterns, increasing surface area and filtration efficacy.
Practical Applications of 3d printed water filter Systems
There are numerous real-world applications where 3d printed water filters are making an impact:
Decentralized Water Purification in Remote Areas
In areas lacking centralized water treatment facilities, affordable and customizable 3D printed filters offer a vital solution to improve public health and access to clean water.
Rapid Prototyping for Industrial Use
Industries requiring specific filtration solutions can leverage 3D printing to develop prototypes quickly, optimize designs, and scale production efficiently.
Point-of-Use Home Filtration
Homeowners can benefit from personalized water filter components tailored to their local tap water chemistry, including filters optimized for removing specific contaminants like lead, chlorine, or pesticides.
Emergency and Disaster Relief
Portable, easy-to-produce 3D printed water filters are invaluable during crises where traditional manufacturing might be too slow or unavailable.
Innovative Materials for 3D Printed Water Filters
The choice of material is crucial for the effectiveness and longevity of 3D printed water filters. Some promising materials include:
- Porous Ceramics: Known for their robustness and excellent filtration of microorganisms and particulates.
- Biodegradable Polymers: Such as PLA, used for eco-friendly filters that decompose after their lifespan.
- Functionalized Polymers: Polymers infused with antimicrobial agents or photocatalytic properties to enhance contaminant removal.
- Recycled Plastics: Promoting sustainability by repurposing waste plastics into functional filters.
The Manufacturing Process of 3d printed water filter Components
Developing a high-quality 3D printed water filter involves several stages:
Design and Modeling
Using sophisticated CAD software, designers create detailed models that specify pore size, channel geometry, and other features essential for optimal filtration.
Material Selection and Preparation
Choosing the right filament or slurry compatible with the desired application, considering factors like chemical resistance, porosity, and strength.
Printing and Post-Processing
The object is printed using precise additive manufacturing techniques such as stereolithography (SLA), digital light processing (DLP), or fused deposition modeling (FDM). Post-processing steps like curing, cleaning, or surface finishing ensure the filter's final performance and durability.
Testing and Validation
Rigorous tests for flow rate, filtration efficiency, lifespan, and contaminant removal are essential before deploying the filter in real-world scenarios.
Future Trends in 3D Printing for Water Filtration
As 3D printing technology evolves, several exciting trends are expected to shape the future of water filtration:
- Multi-Functional Filters: Combining filtration with sensors for real-time monitoring of water quality.
- Self-Healing Materials: Innovations in self-repairing polymers to extend filter lifespan.
- Nanomaterial Integration: Embedding nanomaterials like graphene or silver nanoparticles for enhanced antimicrobial and filtration properties.
- Distributed Manufacturing: Enabling local communities to produce their own filters on demand, reducing reliance on global supply chains.
- Sustainable and Eco-Conscious Designs: Focus on zero-waste manufacturing and biodegradable components to minimize environmental impact.
Challenges and Considerations in Developing 3D Printed Water Filters
While the potential is immense, practitioners and developers face certain hurdles:
- Material Limitations: Not all materials suitable for 3D printing are equally effective for water filtration, necessitating ongoing research and development.
- Scale-Up Difficulties: Transitioning from prototyping to mass production involves technical and economic challenges.
- Regulatory Compliance: Ensuring that 3D printed filters meet safety standards for potable water is essential.
- Long-Term Durability: Maintaining performance over extended periods, especially in diverse environmental conditions, is critical.
- Cost Considerations: Balancing the innovation costs with affordability remains a key concern for widespread adoption.
Conclusion: Embracing Innovation for a Sustainable Water Future
The integration of 3D printing into water filtration technology heralds a new era of sustainable, affordable, and highly effective solutions. The 3d printed water filter exemplifies how technological innovation can address pressing global challenges related to access to clean water. As research advances and manufacturing becomes more refined, these filters will play an increasingly vital role in ensuring healthier lives, especially in underserved regions worldwide.
Businesses and entrepreneurs, such as 3dprintwig.com, are at the forefront of this revolution, pushing the boundaries of what is possible with 3D printing. From creating prototype designs to deploying scalable solutions, the future of water filtration is undeniably intertwined with the transformative power of additive manufacturing.
Investing in and adopting these innovative filtration solutions not only promotes environmental sustainability but also offers a strategic advantage in meeting the growing global demand for clean, safe drinking water. The era of 3D printed water filters has arrived, and it promises a brighter, healthier future for all.